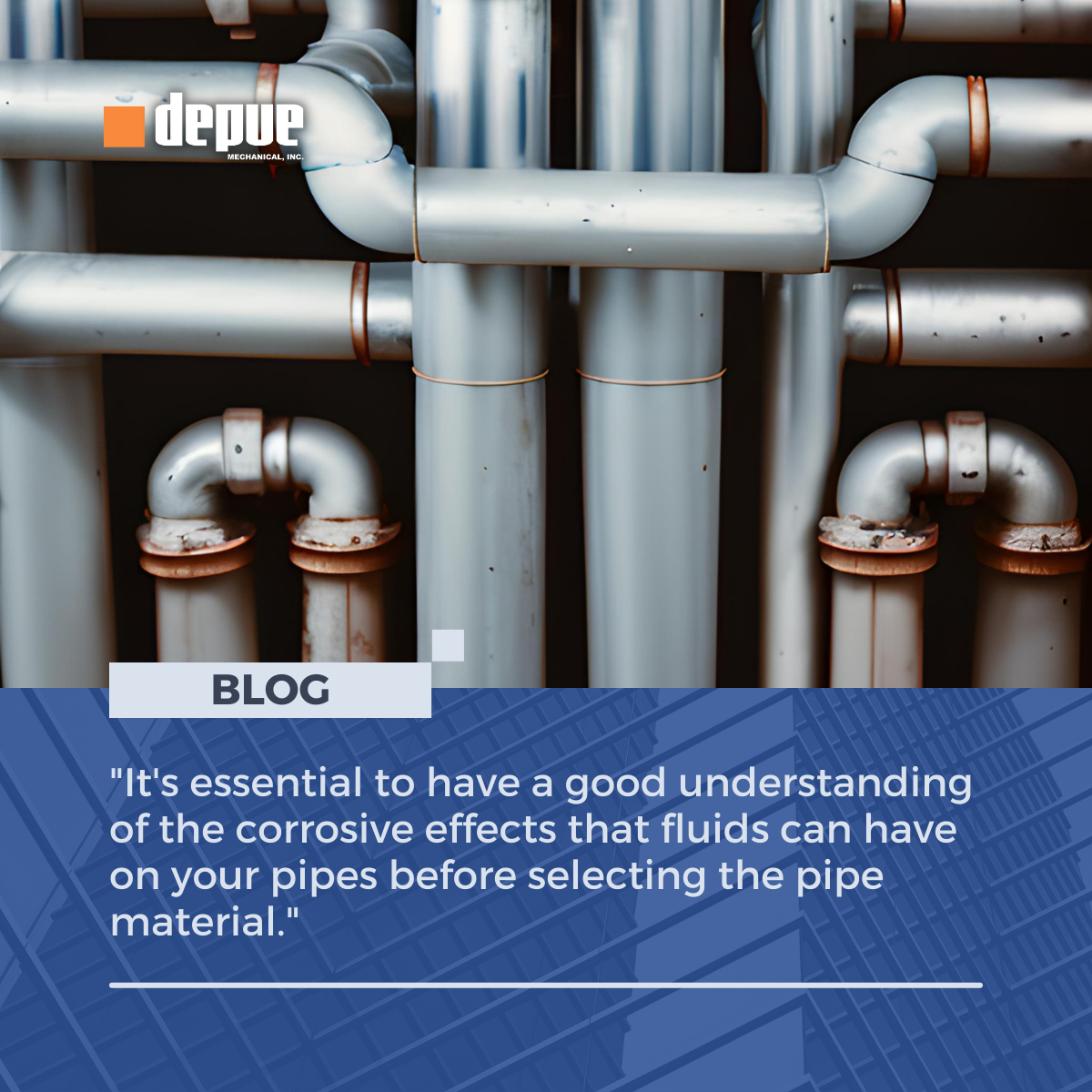
Your Pipe Material is Important
In industrial facilities and manufacturing plants, the fluid handling system is a crucial component for success. Over time, the pipes and fittings in the system may need repair or replacement, and selecting the right pipe material is vital. Whether you’re building a new facility or replacing an existing fluid handling system, choosing the right pipe material to transport your liquids, chemicals, gases, and other fluids is a critical decision. Rushing into this decision could put your product quality, production times, and employee safety at risk. Therefore, it’s essential to have a good understanding of the corrosive effects that fluids can have on your pipes before selecting the pipe material.
Understanding Corrosive Liquids’ Effect on Pipe Material
Are you aware of the liquid being transported through your pipes? Specifically, is it a corrosive or non-corrosive liquid? Corrosive liquids, such as hydrogen chloride, crude oil, seawater, and other acidic liquids with strong chemical properties, require a pipe material that is resistant to corrosion. On the other hand, non-corrosive gases or fluids, such as nitrogen, water, and lube oil, can be safely transported using carbon steel or metal pipelining.
With these items in mind, here are the 10 best and worst corrosion-resistant pipe materials for your fluid handling system:
- Cast iron: Cast iron is easy to find and impeccably strong. It is much safer than most pipes due to it’s resistance to fire and other external sources of corrosion, like plant growth and soil, because it is so thick. Cast iron is capable of enduring water and saltwater temporarily, making it a possible option for brief assignments. Nonetheless, it deteriorates and oxidizes when exposed to water for extended periods of time.
- Copper: Copper has been a popular material in various industries due to its accessibility and attractive appearance. Although copper is not entirely resistant to corrosion, it fares better compared to other materials like galvanized steel. However, copper is most vulnerable to corrosion when exposed to fresh and saltwater, as well as harsh chemicals and acids. Knowing these characteristics of copper can help in its proper application and maintenance to ensure its longevity.
- Stainless steel: Stainless steel is aptly named as it has the ability to resist rust and corrosion more effectively than other materials. This is due to its composition of multiple alloys that work together to create a protective oxide layer on the surface. This layer is not only natural but also strong and durable, providing lasting protection. Because of this, stainless steel is an excellent choice for water pipes, as well as for use with certain oils and chemicals. Understanding the unique properties of stainless steel can help in selecting the appropriate material for different applications.
- Carbon steel: While carbon steel may be a suitable option for fluids with high temperatures, it is prone to corrosion when exposed to high levels of moisture, chemicals, and acids.
- Galvanized steel: If you’re working on a short-term project in saltwater environments, galvanized steel is a good choice for pipe material because it doesn’t rust. However, if it is exposed to salt and water for extended periods, it will eventually corrode. It’s also important to keep in mind that galvanized steel tends to corrode from the inside out, making it difficult to detect.
- Aluminum alloy:Aluminum is a great choice when you need to transport liquids without the risk of rust contamination. It is resistant to many gases, oils, and liquids, making it a reliable option. However, aluminum is still susceptible to corrosion over time, particularly in environments with saltwater or sulfuric applications.
- Polypropylene (PP) lining: PP-lined pipe is an excellent choice for high-temperature applications, withstanding temperatures as high as 225 degrees and suitable for use with saltwater, basic, and acidic materials. However, it is not capable of withstanding solvents, volatile organic compounds (VOCs), or extremely low temperatures. PP lining is commonly used in various industries, including water treatment, chemical processing, power generation, and food and beverage manufacturing.
- Fluoropolymer (PTFE) lining: PTFE-lined pipe is an extremely versatile material that is non-reactive and highly resistant to corrosive chemicals. It can be applied to a wide range of applications and is well-known for its durability and zero-risk of product contamination. This makes it an ideal choice for pipes that handle various materials such as acids, water, chemicals, and oils.
- ATL PTFE lining: ATL PTFE-lined pipe is composed of specifically formulated resins that make it incredibly strong and durable, even in harsh environments with prolonged exposure to saltwater and aggressive chemicals. This makes it a popular choice in industries such as paper processing, power generation, and the service industry.
- PVDF lining: PVDF-lined pipe is highly durable and incredibly strong, making it one of the most abrasion-resistant materials available. This lining is an excellent option for manufacturing facilities or plants that handle high-strength acids, chemicals, saltwater, and even nuclear materials. Additionally, PVDF lining is resistant to corrosion from natural sunlight and weathering, making it a reliable choice for outdoor applications.
The nature of the liquid or gas that a pipe system will transport is a crucial factor in selecting the appropriate fluid handling pipe material. While certain pipe materials may be suitable for non-corrosive liquids such as oils or standard wastewater, more corrosive liquids like acid or peroxide require a pipe with a robust interior that can withstand the abrasive effects of these corrosive materials. Such corrosive materials are commonly found in many industrial cleaning solutions, as well as in chemical manufacturing and handling. Despite a plastic or metal pipe material’s durability and corrosion resistance, it’s worth noting that chemicals, acids, and saltwater are far more abrasive than standard water or oil. Therefore, it’s vital to consider the liquid you’ll be transporting when choosing a pipe material.
Not sure what pipes are best for your fluid handling system? Connect with us.